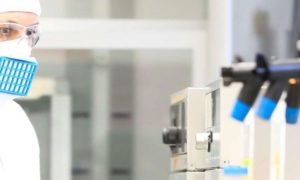
In the COVID-19 pandemic prevention tests, paper curtains are increasingly mandatory. Their relative effectiveness is no longer questioned, but their widespread use has many disadvantages. This includes the environmental impact of disposable masks made from non-woven polypropylene microfiber plastic coating. In addition, they only catch pathogens instead of destroying them. “In a hospital environment, these masks are placed in special containers and handled (Filter ‘paper’ made from titanium oxide nanowires) well,” said László Forró, head of the EPFL’s Physics or Complex Materials Laboratory. “Use in the wider world – where they are deposited in open landfills and even left on the road – could create new sources of pollution.”
Forró’s researchers are working on a good solution to this problem: a membrane made of titanium dioxide (Filter ‘paper’ made from titanium oxide nanowires) nanotrades, similar to filter paper, but with antibacterial and antiviral properties.
Their material works using the photocatalytic properties of titanium dioxide. Upon exposure to ultraviolet radiation, the fibers convert moisture into living oxidizing agents, such as hydrogen peroxide, which have the ability to kill pathogens. “Because our filter absorbs moisture so well, it can catch droplets that carry viruses and bacteria,” Forró said. “It provides a favorable environment for the oxidation process that is caused by light.”
Researchers’ work can now be found in Advanced Functional Materials and includes experiments that demonstrate the ability of the E membrane. Coli, reference bacteria in biomedical research, and DNA strands in seconds. Based on these results, the researchers concluded – although still experimental – that the process could be just as successful for a wide range of viruses, including SARS-CoV-2.
Her article also states that the production of such membranes can be done on a large scale: only laboratory equipment can produce up to 200 m2 of filter paper per week, enough for a maximum of 80,000 masks per month. In addition, the masks can be sterilized and reused a thousand times. This can reduce imperfections and reduce the amount of waste generated by disposable surgical masks. Finally, the manufacturing process, which involves the calcination of titanite nanowires, makes them durable and avoids the risk of user detection of nanoparticles.
A startup called Swoxid is ready to move the technology out of the lab. “Membranes can also be used in air conditioning applications, such as ventilation and air conditioning systems, as well as personal protective equipment,” said Endre Horváth, lead author and co-founder of Swoxid.