By Dr Yashwant Mahajan
Introduction
It is generally well known that a significant amount of energy is lost due to friction in sliding interfaces. Therefore, exploring novel approaches to minimize friction and wear through new technologies in tribology is of paramount importance to build a greener and more sustainable world. It has been estimated that 23% (119 EJ0 of the overall global energy consumption originates from tribological contacts (Influence of tribology on global energy consumption, costs and emissions). Out of which, about 20% (103EJ) is used to overcome friction.
Restraining friction and wear is a global issue because it is interrelated with an expanded range of material applications from simple tools to industrial machine components, biomedical devices, microelectrochemical systems (MEMS), and nanoelectromechanical systems (NEMS). Approaches such as utilizing new materials (including nanomaterials), surface modification and novel lubrication technologies are being intensively pursued to reduce friction and wear in various systems all over the world, it is projected that energy losses due to friction and wear could potentially be reduced by 40% in the long term (15 years)and by 18% in the short term (8 years)(Influence of tribology on global energy consumption, costs and emissions).
Nanomaterials have been acknowledged as potential nanoscalesolid lubricant films and lubricant additives. They offer significant advantages as compared to conventional organic molecules (For example: zinc dialkyldithiophosphate (ZDDP), chlorinated paraffins, sulfurized lard oils, phosphate esters, over-based calcium sulfonates etc.) being currently used as lubricant additives. Nanomaterials additives have theenormous potential in enhancing lubricity, overcoming frictional effects, reducing wear and tear, and augmenting load bearing capacity and,in turn, saving energy, increasing the efficiency of dynamic transmission, dampening vibrations,promote eco-friendly environment (as compared to conventional organic molecular additives) and reducing noise.
The key features of the nanoparticle lubricant additives, which are responsible to upgrade the performance of the conventional lubricants are the nano-scale effects, thermal stability, diverse particle chemistries and superior tribological characteristics (Nanotechnology implications for high performance lubricants). The important commercial nano-lubricant additives are WS2 (multi-layered fullerene shaped nanospheres), detonation nanodiamond, boron, MoS2, copper. SiO2, CuO and so on.
Introduction to Friction and Super lubrication
Every moving system being used by humanity consumes enormous amount of energy due to frictional losses. Therefore, researchers around the world are still exploring innovative ways to minimize the undesirable impact of friction to a negligible level (nearly zero friction). This is referred to as super -lubricity (Reduction of coefficient of friction to near-zero values, below 0.01) (Figure 1).
Figure 1 –Coefficient of Friction (COF) range in super lubricity region.(Wang, H., Liu, Y. Superlubricity achieved with two-dimensional nano-additives to liquid lubricants. Friction 8, 1007–1024 (2020). https://doi.org/10.1007/s40544-020-0410-3).
Creative Commons AttributionAttribution 4.0 International (CC BY 4.0).
The super lubricity is one to two magnitude orders lower than the friction coefficient of about 0.1 of the conventional solid lubricating material. Therefore, the development of the super-lubrication technology not only has profound significance for saving energy, reducing consumption and promoting national economy, but also can stimulate remarkable progress pertaining to the design and operation reliability of high-technology equipment.
In 1990, Hirano and Shinjo, Japanese researchers, first predicted a friction-free state (Atomistic locking and friction), where sliding resistance and wear between friction pairs virtually vanish, since then,the term “super-lubricity” began to be formally defined, which is known as solid super-lubricity or structural super-lubricity, afterwards.Subsequently, this hypothesis was confirmed by a series of experiments during 1991-1997, (Anisotropy of frictional forces in muscovite mica, Super-lubricity of molybdenum disulphide, Observation of superlubricity by scanning tunneling microscopy).
In the year 2004, a team of researchers from The Netherlands have experimentally demonstrated the superlubricity (Superlubricity of Graphite) in another lamellar material graphite and their results conclusively validated Hirano’s model of superlubricity.The super-lubricity can also occur under ultra-high vacuum and it was first experimentally observed by Martin in 1993 through a macroscale sliding contact of MoS2 coatings (Superlubricity of molybdenum disulphide). While initial research focus was on nano- and micron-scales, now there is growing interest in larger scale tests for high-pressure industrial applications (Structural super-lubricity and ultralow friction across the length scales).
The discovery of two-dimensional (2D) analogs of graphite, MoS2, WS2, GO, hexagonal BN, and many other layered materials has transformed and revitalized the field of tribology(Graphene: a new emerging lubricant). It has been demonstrated that these 2D materials, with only one or a few atomic layers, can reduce friction coefficient well below 0.01, which falls under the regime of “superlubricity” (Approaches for Achieving Superlubricity in Two-Dimensional Materials).
Although realizing structural superlubricity across multiple length and load scales has been very challenging task in the past, the ground breaking studies carried out by the researchers at Argone National Laboratory have recently combined 2D materials with nano-carbon materials and observed superlubric sliding expanding well into the macro- and meso-scales (Macroscalesuperlubricity enabled by graphenenanoscroll formation).
The realm of superlubricity is mainly divided into three main categories based on their characteristics, i.e., solid superlubricity, liquid superlubricity, and solid-liquid combined superlubricity (SLCS). The solid superlubricity arises when the lubrication occurs in the absence of liquid, in which contact pressures of 1 GPa have been achieved for the microscale and 2.5 GPa at the nanoscale (Superlubricity under ultrahigh contact pressure enabled by partially oxidized black phosphorus nanosheets).
As reported by Berman et al. (Approaches for Achieving Superlubricity in Two-Dimensional Materials)a number of mechanisms are operative for frictional energy dissipation during the sliding processas schematically shown in Figure 2, including wear (shear and removal of material from sliding surfaces), molecular deformation (elastoplastic surface deformation), thermal effects (thermally activated energy barriers), electronic effects (static electricity build-up which can influence frictional effects), bonding (formation of the chemical bonds—at atomic/molecular levels—between sliding surfaces or top layer and substrate), phonons (energy dissipation through lattice vibrations), environment/chemistry (surface functionalization/ surrounding atmosphere), and structural effects (atoms locking on commensurate surfaces).
Figure – 2. Representative schematics of possible mechanisms for energy dissipation during sliding: (a) wear, (b) molecular deformation, (c) thermal effect, (d) electronic effect, (e) bonding, (f) phonons, (g) environment/chemistry, and (h) structural effect.
Reprinted with permission from (Approaches for Achieving Superlubricity in Two-Dimensional Materials, Diana Berman, Ali Erdemir, Anirudha V. Sumant, ACS Nano, American Chemical SocietyMar 1, 2018) Copyright © 2018, American Chemical Society
Apart from their unique dry lubrication performance, 2D materials also exhibit superior anti-friction and anti-wear properties as additives in industrial lubricants or composites (Tribology of two-dimensional materials: From mechanisms to modulating strategies). For example, Y. Cho et al. have demonstrated that even the infinitesimal amounts of (0.05 and 0.01 wt%) h-BN nano-sheets additive in water can reduce friction and wear for an extended length of time irrespective of the amount of h-BN nano-sheets. It was concluded that the repeated exfoliation and deposition of h-BN occurred on the sliding surfaces, forming tribo-films which can result in reduction of friction and wear.
Based on the above-mentionedfacts, the h-BN nano-sheets, which can be simply and inexpensively dispersed, can be apromising candidate material as ‘‘green’’ lubricant additive in water. (Evaluation of hexagonal boron nitride nano-sheets as a lubricant additive in water). By adding MoS2 nanosheets into hydraulic oil, Zhao et al. reported that the friction coefficient could be decreased to 0.04, which is essential for lubrication of electro-hydrostatic actuators (EHA) (An investigation on the tribological properties of multilayer graphene and MoS2 nanosheets as additives used in hydraulic applications).At larger scales required for most commercial and medical applications, liquid superlubricity offers greater potential, but so far, contact pressures have been limited to below 0.3GPa.
A form of phosphorus, 2D black phosphorus (The rising star of 2D black phosphorus beyond graphene: synthesis, properties and electronic applications) can also form molecular-thin sheets. A recent publication (Superlubricity of Black Phosphorus as Lubricant Additive) shows that when coated in water, the sheets help to achieve liquid superlubricity. Research in the field has faced obstacles in reaching liquid superlubricity at an ultrahigh contact pressure, but the recentstudy demonstrated that superlubricity can be realised under a contact pressure of 1193 MPa with lubricated partially oxidized black phosphorus nanosheets (Superlubricity under ultrahigh contact pressure enabled by partially oxidized black phosphorus nanosheets).
Like graphene, the black phosphorus material is also layered, but especially, attracts significant amount of water, where each sheet holds onto water molecules across its area. When the solids slide against each other, so do the water layers with very low friction. These slippery liquid layers resist pressure when squeezed, achieving superlubricity under ultrahigh contact pressures, offering potential for diverse industrial uses.
As mentioned earlier paragraph, SLCS is a newly proposed method (Superlubricitive engineering—Future industry nearly getting rid of wear and frictional energy consumption), which refers to the manner in which a superlubricity state is formed by mixing surface-modified 2D materials into liquid lubricants, and the 2D materials and liquid molecules function together in the friction process. Research has shown that SLCS can significantly enhance the load-bearing capacity of the superlubricity system, even up to the gigapascals (GPa) order of magnitude (Black phosphorus as a new lubricant), which paves a new way for industrial application.The prime example of SLCS is presented in the work carried out by the researchers at Tsinghua University (Macroscalesuperlubricity under extreme pressure enabled by the combination of graphene-oxide nanosheets with ionic liquid), wherein, a robust macroscale liquid-superlubricity state (μ ≈ 0.005) under an extreme pressure of 600 MPa could be achieved, which was enabled by the combination of graphene-oxide (GO) nanosheets with an ionic liquid (IL) between the frictional pairs of Si3N4/sapphire.
On the basis of research in the area of SLCS, Luo and Zhou (Superlubricitive engineering—Future industry nearly getting rid of wear and frictional energy consumption) forecastedthe application opportunities of superlubricity in industry. They proposed a number of industrial applications ofsuperlubricity, which include transmission parts, such as gearboxes, clutches and bearings; components for high-speed and heavy-duty trains; aviation components; shipping industry-engine wear parts; fluid machinery used in the fields of hydraulic, pneumatic, and sealing industries; manufacturing; aerospace; Microelectromechanical systems (MEMS), renewable energylike gears in a wind turbine and so on. They estimated that the economic benefits of superlubricity can reach trillions of US dollars per year.
Another important issue of great concern in the field of tribology is how to promote eco-friendly environment to achieve sustainable development. In recent times, water-based nano lubricant additivesare being developed as promising eco-friendly lubricants by dispersing nano additives into water, which combines superior cooling capacity of water with excellent lubricity contributed by the nano additives.
The use of water-based nano lubricants not only provides protection against friction and wear between the tool and the workpiece, but also improves overall quality of the product, demonstrating a great potential in engineering applications, such as metal forming. This subject has been comprehensively dealt by the researchers from University of Wollongong (A Comprehensive Review of Water-Based Nanolubricants).
Introduction to MXene Materials–
2D materials possess extraordinary electronic, mechanical and optical properties (Recent Advances in Two-Dimensional Materials beyond Graphene), which have elicited immense interest among the scientific community across the globe to pursue extensive studies in the past decade for diverse applications.2 D materials can also function as convenient building blocks for a range of layered structures, membranes and composites (2D materials and van der Waals heterostructures). Although, several single-element 2D materials have been prepared, such as graphene, silicene , germanene and phosphorene (Single-Element 2D Materials beyond Graphene: Methods of Epitaxial Synthesis), the majority contain two (for example, dichalcogenides and oxides) (Stable, Single-Layer MX2 Transition-Metal Oxides and Dichalcogenides in a Honeycomb-Like Structure) or more elements (for example, clays).
MXenes are a class of two-dimensional, 2D inorganic compounds. These materials comprise a-few-atoms-thick layers of transition metal carbides, nitrides, or carbonitrides that are made by selectively etching MAX phases.The first MXene, Ti3C2, was synthesized by Michel Naguib, a former PhD student and current professor at Tulane, advised by Prof. Michel Barsoum and Prof. YuryGogotsi, in 2010 and their work was published in 2011., it wasn’t until 2017 that the MXene’s true potential was realized and researchers started intensively researching to discover new MXenes at an unprecedented rate. MXenes combine the metallic conductivity of transition metal carbides with a hydrophilic nature because of their hydroxyl- or oxygen-terminated surfaces (Two-Dimensional Nanocrystals Produced by Exfoliation of Ti3AlC2, 25th Anniversary Article: MXenes: A New Family of Two-Dimensional Materials).
As on date, about 50 MXenes with various combinations of metal, carbon, and nitrogen atoms, as well as surface functional groups, such as oxygen or halogens, have been reported. The ultimate number is far greater and in time they may develop into the largest family of 2D materials known. MXene’s astonishing properties, such as their metal-like electrical conductivity reaching ≈24 000 S cm-1, render them quite useful in a large number of applications (Improved synthesis of Ti3C2Tx MXenes resulting in exceptional electrical conductivity, high synthesis yield, and enhanced capacitance).
MXenes are noteworthy for their distinctive properties that combine aspects of both metals and ceramics. These include excellent thermal and electrical conductivity, heat resistance, easy machinability, high mechanical flexibility and stiffness (up to 386 ± 13 GPa for Nb4C3Tx)) (Electrical and Elastic Properties of Individual Single-Layer Nb4C3Tx MXene Flakes), catalytic activity, high strength and excellent volumetric capacitance, having the highest EMI shielding effectiveness of all similar synthetic 2D materials, and tunablehydrophobic nature due to the presence of various surface functional groups.
MXenes, as conductive layered materials with tunable surface terminations, have been shown to be promising candidates for energy storage applications (Li-ion batteries, supercapacitors, and energy storage components), composites, photocatalysis, water purification, gas sensors, transparent conducting electrodes, neural electrodes, as a metamaterial, SERS substrate,photonic diode, electrochromic device, biomedical devices and triboelectric nanogenerator (TENGs), to name a few (MXenes-wikipedia).
Though the basic definition of MXenes as 2D transition metal carbides and nitrides is straightforward, there is enough variety in structures and compositions that defining terminology for MXenes is necessary when discussing them in detail.
Figure – 3: General element composition of MAX phase and MXene: M: early transition metal, A: Group A element, X: C and/or N, Tx:
surface functional group(Zamhuri, A., Lim, G.P., Ma, N.L. et al. MXene in the lens of biomedical engineering: synthesis, applications and future outlook. BioMedEngOnLine 20, 33 (2021). https://doi.org/10.1186/s12938-021-00873-9). Creative Commons Attribution 4.0 International (CC BY 4.0)
Today, MXenes are an ever-expanding field of 2D transition metal carbides and nitrides. Ternary MAX phase compounds with the formula Mn+1AXn (e. g., Ti3AlC2) are the precursors for the synthesis of MXenes (e. g., Ti3C2Tx), where M is a transition metal, A is an element such as aluminium or silicon, and X is either carbon or nitrogen, with n=1, 2, or 3 (Figure 3). Producing the 2D MXenefrom the bulk three-dimensional MAX phase compound involves exfoliation or etchingusing strong etching solutions such as HF, a mixture of fluoride salts and various acids, non-aqueous etchants, halogens, and molten salts etc. to selectively remove the A layer (Figure 4), resulting in carbide or nitride layers just a few atoms thick, which can be separated by other ions(known as intercalation) which can enhance their properties.The selective etching results in the formation of surface groups (shown as Tx) from their etching solution, which are commonly-O, -F, -(OH).
Figure –4: Schematic illustration of top-down MXene synthesis process (acid exfoliation method). (Zamhuri, A., Lim, G.P., Ma, N.L. et al. MXene in the lens of biomedical engineering: synthesis, applications and future outlook. BioMedEngOnLine 20, 33 (2021). https://doi.org/10.1186/s12938-021-00873-9). Creative Commons Attribution 4.0 International (CC BY 4.0)
Friction, Wear and Lubrication in MXene Materials
The tribology and mechanical property of MXene flakes are of crucial importance because they can be used as shown in Figure 5 either as solid lubricants orlubricant additives (Preparation and Tribological Properties of Ti3C2(OH)2 Nanosheets as Additives in Base Oil) or considered as a reinforcing agent in a metallic/polymeric based composite material (Mechanotribological Aspects of MXene-Reinforced Nanocomposites).
Figure – 5:Tribological application of MXenes including lubricant additives, solid lubricant films, and composite additives.
Reprinted with permission from (Computational Study of Low Interlayer Friction in Tin 1Cn (n = 1, 2, and 3) MXene, Difan Zhang, Michael Ashton, AlirezaOstadhossein, et al., Applied Materials, American Chemical Society, Oct 1, 2017) Copyright © 2017, American Chemical Society
MXenes are particularly interesting for tribological applications due to their wide possible compositions and forms along with graphite-like structure, presence of low shear strength arising due to very weak van der Waals interlayer interactions between adjacent layers, stiff-in-plain bonding characteristicsand self-lubrication ability (Two-dimensional Ti3C2 coating as an emerging protective solid-lubricant for tribology). Moreover, theyare promising candidates for tribological applications because of their superb mechanical strength, superior wear resistance and bending rigidity (Elastic properties of 2D Ti3C2Tx MXene monolayers and bilayers) and there is enough scope for having a precise control over the monolayer thickness (Electrophoretic deposition of two-dimensional titanium carbide (MXene) thick films).
The low COF can be ascribed partly due to the presence of low energy barrier stems from TX-TX interactions toward interlayer sliding. Density functional calculations and molecular dynamic simulations (Computational Study of Low Interlayer Friction in Tin+1Cn (n = 1, 2, and 3) MXene) assessing the tribological properties of MXenes revealed that the frictional properties between different layers depend on M-X composition, stoichiometry and surface terminations. Computational studies reported for Ti-based MXenes that Ti2CO2 has a sliding barrier of 0.017 eV while bare Ti2C (with no surface terminations) has a sliding barrier of 0.237 eV, thus approaching energy barrier values of graphene (0.002 eV) (Stacking stability and sliding mechanism in weakly bonded 2D transition metal carbides by van der Waals force), which corresponds to COFs of 0.24–0.27 for bare titanium based MXenes while O-terminated titanium-based MXenes have COFs of 0.10–0.14((Computational Study of Low Interlayer Friction in Tin+1Cn (n = 1, 2, and 3) MXene)respectively.The calculated values for MXenesindicate promising frictional, and possibly possess interesting wear characteristics, which may help to overcome important drawbacks of conventional solid lubricants. (Tribology of two-dimensional materials: From mechanisms to modulating strategies).
MXenesas Solid Lubricants
Recently, WeiqiLian et al. (Two-Dimensional Ti3C2 coating as an emerging protective solid-lubricant for tribology) have investigated wear and friction properties steel ball against bare copper or copper coated Ti3C2 coatings to evaluate their potential as solid lubricants. The wear rate and coefficient of friction of the Ti3C2 coatings modified copper surface are respectively about one tenth and one fourth of the bare copper. Their findings revealthat carbon-rich lubricating transferred film is generated by the friction-induced graphitization. The transferred film not only has inhibiting effect between the sliding contact interfaces, but also generate lubricating graphite, resulting in the friction and wear reduction. The resultsof this study show that Ti3C2 exhibits a huge potential application as an emerging solid-lubricant for sliding friction.
In a study jointly conducted by the researchers from Chile, Germany and China (Multi-layer Ti3C2Tx-nanoparticles (MXenes) as solid lubricants – Role of surface terminations and intercalated water), they have addressed for the first time the influence of surface terminations and intercalated water in Ti3C2Tx-nanoparticles on friction and wear when used as a solid lubricant. Ball-on-disk experiments at 4% relative humidity reveal excellent tribological properties of these Ti3C2Tx-nanoparticles with a remarkable friction reduction of about 300% (Steady state COF for the steel-alumina pair is 0.7, whereas the steady state COF for Ti3C2Tx coated sample is about 0.17) along with the potential to greatly reduce adhesive, abrasive and tribo-chemical wear.This study points out the significant influence of surface terminations and intercalated water, defining them as the key parameters to tailor the resulting frictional performance. Consequently, their results highlight Ti3C2Tx -nanoparticles as outstanding, next-generation solid lubricants in nano- and micro-scale systems.
Until recently, the tribological studies on MXenes have mainly directed towards titanium-based MXenes (mainly Ti3C2 Tx nano-sheets), and the fundamental effects/mechanisms were investigated mainly by laboratory model tests under pure sliding motion. When this knowledge is transferred to macro-scale and application-oriented conditions with more complex geometries, kinematics and stresses, the underlying mechanisms are yet to be explored (An investigation of material and tribological properties of Sb2O3/Au-doped MoS2 solid lubricant films under sliding and rolling contact in different environments).In view of this in real life situation, Marian et al. (MXenenanosheets as an emerging solid lubricant for machine elements – Towards increased energy efficiency and service life) applied MXenenano-sheets as solid lubricants to highly loaded rolling-sliding contacts of machine elements. In component level testing, an up to 3.2-fold friction reduction, a decrease in the cumulative linear wear by 2.9 times, and an extension of service life by a factor of 2.1 were observed for Ti3C2Tx coated thrust ball bearings, in comparison with uncoated references. This demonstrates the potential of MXenes to lubricate dry-running machine elements effectively and efficiently.
In a recent study (Ti3C2Tx Solid Lubricant Coatings in Rolling Bearings with Remarkable Performance beyond State-of-the-Art Materials),MXenes’ tribological response is compared with state-of-the-art solid lubricant coatings, including molybdenum disulfide (MoS2), tungsten-doped hydrogenated amorphous carbon (a-C:H: W), and hydrogen-free, more graphite-like amorphous carbon (a-C). It was found that multi-layer Ti3C2Tx-MXene coatings reduce wear on the bearing washers by up to 94 %relative to uncoated references,which was comparable to DLC coatings and even superior to MoS2 coatings.
The excellent performance of MXene coatings can be attributed to the transfer of the lubricious MXenenano-sheets to secondary tribo-contacts (rolling elements and cage pockets) of the bearing. Although,the frictional torque of all solid lubricant coatings is similar during steady-operation, the MXene coated bearings extend the service life span by 30 % and 55 % compared to MoS2 and DLC, respectively. This contribution demonstrates the ability of MXene solid lubricant coatings to outperform state-of-the-art solid lubricants in dry-running machine components such as rolling bearings.
Guo et al. (Nanomechanical Properties of Ti3C2 Mxene) undertook studies to understand nanomechanical (adhesion and friction at nanoscale) behaviour of MXenesas a function of the applied normal force, temperature and pressure by employing atomic force microscopy (AFM). It was found in AFM tests that MXenedisplayed enhanced adhesion and friction at higher pressure but exhibited reduced adhesion and friction at elevated temperature. X-ray photoelectron spectroscopy was used to reveal the change in the chemical structure of MXene at different temperatures.
The researchers found increased oxidation, and replacement of C by O atoms occurred on MXene at elevated temperatures, which has a profound influence on the adhesion and friction between MXene and the probe tip. This discovery lays the foundation for understanding the adhesion mechanism and the dynamic adhesivebehavior in friction of MXene, rendering MXene a much broader application prospect such as MEMS/ NEM’S devices, small scale devices, thrust bearings, machine components and precision mechanical systems and so on.
The nanoscale frictional properties of the isolated Ti3C2TxMXenenanosheets were investigated by P. Pendyala et al. (Layer-dependent frictional properties of Ti3C2Tx MXenenanosheets) using AFM to find out the role of layering in tuning friction. Ti3C2Txnanosheets reduced friction by approximately 50% for monolayer sheets and up to 70% for two-layer and three-layer sheets, compared to the Si substrate. In particular, Ti3C2Txexhibited a layer dependence of friction, with friction force decreasing in response to an increase in the number of layers. The layer-dependent frictional properties were explained using the high degree of elastic compliance of atomically thin Ti3C2Txnanosheets.
An increase in the number of layers reduced the elastic compliance (increase the elastic stiffness), thereby reducing the out-of-plane puckering-type deformation associated with atomically thin 2D nanosheets. Decreased puckering reduces the real contact area between the probe and nanosheet as well as the energy loss owing to the moving deformation zone, thereby lowering the overall friction. Therefore, MXenes with tunable interlayer properties can aid the development of tunable layer-dependent solid-state friction materials.
Chemical functionalization of MXenes could be an excellent approach to enhance the substrate/coating adhesion, which could further augment the tribological performance of hybrids due to stronger surface interactions, as well as creating possible bonding options with other 2D nanomaterials. Additionally, this approach has a potential to considerably enhance their dispersion’s stability (additives) as well as adhesive and interfacial strengths (solid lubricants and composites).
MXenes as Lubricant Additives
The tribological behaviour of the as-prepared 2D Ti3C2 as a lubrication additive in base oil was investigated (Synthesis, characterization, and tribological properties of two-dimensional Ti3C2) by J. Yang et al. Results have established that 2D-layered Ti3C2can greatly enhance the friction-reducing and anti-friction properties of paraffin based oil, especially with a presence of small amount of 1.0 wt% Ti3C2. It was found that the friction coefficient significantly reduced from 0.125 to 0.063 with the additive concentration increasing from 0.0 to 1.0 wt% due to the lamellar structure of Ti3C2 filler (i.e., ≈98.4% reduction in the friction coefficient). Furthermore, it was seen that those worn surfaces filled by Ti3C2 created a tribofilm between the mating contacts. This novel 2D-layered Ti3C2 would be a useful candidate as an additive for lubricating materials for practical applications.
- Gao et al. (DialkylDithiophosphate-Functionalized Ti3C2TxMXeneNanosheets as Effective Lubricant Additives for Antiwear and Friction Reduction) carried out studies on introduction of the commercial lubricating additive DialkylDithiophosphate (DDP), which imparts Ti3C2Txwith excellent anti-wear and friction reduction performance. It was found that the as-prepared DDP- Ti3C2Tx nanosheets display oxidation resistance, thermal stability, good dispersibility, and stability in 500SN base oil, as well as superior tribological performance as additives. Moreover, the load capacity of the 500 SN increases from 150 to 500 N; after adding 0.3 wt % DDP- Ti3C2Tx, the COF reduces from 0.24 to 0.11, and the wear volume loss reduces from 6.27 × 105 to 7.80 × 104 μm3, which is due to the formation of protective film (oxides of Ti, Fe, iron phosphate, and ferrous sulfide) at the interface of friction pairs and the filling effect of nanofragments. This work demonstrates an effective approach for the surface modification of the 2D layered sheet-like nanosheets Ti3C2Txand provides a new insight into the application of MXene as a functionalized nano-additive lubricating material.
- Yong et al. (Synthesis and tribological property of Ti3C2Tx nanosheets) have synthesized Ti3C2Txnanosheets by selective etching of Ti3AlC2with concentrated HF solution. The role of the termination groups produced during HF treatment on the exfoliation degree was deliberated. The tribological property of the prepared Ti3C2Tx nanosheets as additives in PAO8 base oil was measured. The maximum reduction of friction and wear was achieved under additive concentration of 0.8 wt% for the highly exfoliated Ti3C2Tx nanosheets. The different effects of Ti3C2Tx additives on the average friction coefficient and wear volume were analysed, respectively.
The tribological behaviour of Ti3C2(OH)2 nanosheets as additives in base oil were studied by X. Zhang et al. (Preparation and tribological properties of Ti3C2(OH)2 nanosheets as additives in base oil) using a UMT-2 ball-on-disc tribo-tester. Under the controlled conditions, the COF of the base oil containing Ti3C2(OH)2 nanosheets was lower than that of the base oil under 15 N load with 200 rpm, and decreased with increasing mass fraction of Ti3C2(OH)2 nanosheets when it was <1.0 wt%. A combination of sliding friction, and the presence of stable tribofilm on the rubbing surface could explain the improved tribological properties of Ti3C2(OH)2 nanosheets as additives.
Xue et al. (Preparation of TiO2/Ti3C2Tx hybrid nanocomposites and their tribological properties as base oil lubricant additives) fabricated TiO2/Ti3C2Tx hybrid nanocomposites through a liquid-phase reaction route wherein TiO2 was coated on the surface of MXene sheets and then the coated MXene was added into a base oil in order to improve tribological and antifriction properties. The hybrid nanocomposite containing 1.0 wt% TiO2/Ti3C2Tx exhibits the best tribological characteristics with the lowest COF when the applied load and the rotation speed were set as 20 N and 150 rpm, respectively. When the concentration is 1.0 wt%, a uniform shielded tribofilm is created in the contact area reducing shear stresses and smoothening the sliding conditions; on the contrary, the situation get worse when too much coated-MXene was added into the base liquid since the friction coefficient increases to a great extent probably owing to severe nanoparticle agglomeration and that the solid lubricating particles could not easily enter the contact area.
Water-based lubrication has been an attractive proposition on account of its eco-friendly nature and economic advantages. However, practical applications of water-based lubrication are often limited, mainly because of its low viscosity and poor corrosion resistance. The use of additives has been proposed to overcome these limitations. In this work (Assessment of Tribological Properties of Ti3C2 as a Water-Based Lubricant Additive), the tribological characteristics of titanium carbide (Ti3C2) MXenes, as additives for water-based lubrication, were systematically investigated for contact sliding between stainless steel under various normal forces and Ti3C2 concentrations.
Both friction and wear were found to decrease with increasing Ti3C2 concentration up to 5 wt%, and then increased when the concentration was larger than 5 wt%. The results suggest that Ti3C2 flakes prevented direct contact, particularly at the edges of the contact interfaces. It was further shown that the agglomeration of Ti3C2 flakes may have increased the hindering effect when an excessive amount of Ti3C2(e.g., 7 wt%) was added. The reduction in the friction coefficient and wear rate with 5 wt% of Ti3C2 concentration were approximately 20% and 48%, respectively. The outcomes of this work may be helpful in arriving at a better understanding of the tribological properties of Ti3C2 as a feasible water-based lubrication additive.
In one of the recent studies (Regulating the Nb2C nanosheets with different degrees of oxidation in water lubricated sliding toward an excellent tribological performance) friction tests were conducted on Nb2C samples exposed with different degrees of oxidation, and the results indicated that the moderately oxidized Nb2C in water solution displayed excellent tribological behaviour, with the COF decreasing by 90.3% and the wear rate decreasing by 73.1% as compared with pure water. As the oxidation proceeded, the original Nb2C gradually changed into a structure of Nb2C/Nb2O5/C.
The Nb2O5 nanoparticles filled in the worn zone and the layered Nb2C and C adsorbed on the surface of the friction pair to form a lubricating film, and their combined action resulted in excellent lubrication. Meanwhile, it was found that the lubrication property of Nb2C was always better than that of pure water, regardless of its degree of oxidation. Based on these findings, significant reduction in friction and wear resistance of moderately oxidized Nb2C display great potential as a nanoadditive in the application of water lubrication technology.
MXene as a Superlubritive
In a recent study (Two-dimensional molybdenum carbide (MXene) as an efficient nanoadditive for achieving superlubricity under ultrahigh pressure) carried out by S. Yi et al., a robust macroscale liquid super-lubricity with a COF of 0.004 was achieved by introducing molybdenum carbide (Mo2CTx) MXene nanoparticles as lubricating additives in a lithium hexafluorophosphate-based ionic liquid at Si3N4–sapphire interfaces.
The maximal contact pressure in the superlubricity state could reach 1.42 GPa, which far exceeds the limit of the superlubricity regime in previous studies. The results indicate that a composite tribofilm (mainly containing molybdenum oxide and phosphorus oxide) that formed at the interface by a tribo-chemical reaction contributed to the excellent anti-wear performance. Furthermore, the extremely low shear strength of the tribofilm and the interlayers of Mo2CTxMXene contributed to the superlubricity. This work demonstrates the promising potential of Mo2CTxMXene in improving superlubricity properties, which could promote the application of superlubricity in mechanical systems.
In another study (In-situ formation of tribofilm with Ti3C2Tx MXenenanoflakes triggers macroscalesuperlubricity), a robust macroscalesuperlubricity state was achieved with COF of 0.002 by introducing Ti3C2TxMXenenanoflakes in glycerol at Si3N4/sapphire interfaces. The MXene-glycerol solution results in the reduction of COF by 96.90 % and 97.87 % compared to those of pristine glycerol and Ti3C2TxMXene solutions, respectively. The friction reduction of MXene-glycerol is attributed to the in-situ formation of tribofilmthat contains colloidal silicon oxides and titanium oxides on the Si3N4 surface. The exceedingly low shear strength of the tribofilms and the synergistic lubrication effect with glycerol dominatesand provides a new technique to realize robust macroscalesuperlubricity via the combined effect of Ti3C2TxMXene and liquid molecules.
In a recent work carried out by S. Huang et al. (Achieving superlubricity with 2D transition metal carbides (MXenes) and MXene/graphene coatings) investigated the tribological properties of two-dimensional titanium carbide Ti3C2-MXene deposited on SiO2-coated silicon (Si) substrates and subjected it to wear by sliding against a diamondlike carbon (DLC)-coated steel ball counter-body using a ball-on-disc tribometer. The researchers have observed that a reduction of the friction coefficient to the superlubric regime (0.0067 ± 0.0017) can be achieved with Ti3C2-MXene alone in dry nitrogen environment. As shown in Figure 6 (b). The COF value for Ti3C2 is 3.3 times lower than that for the Si substrate. Failure points at ~1800 s and 3100 s for the Si substrate and Ti3C2 coating respectively (Figure 6 (a)), are due to wearing out of DLC coating on the ball.
Figure – 6: (a) Tribological behaviour of Si substrate and Ti3C2 on Si substrate against a DLC-coated steel ball and; (b) comparison of COF values demonstrating the onset of superlubricity. Error bars represent standard deviations of the average COF values. (Achieving superlubricity with 2D transition metal carbides (MXenes) and MXene/graphene coatingsS. Huang,K.C. Mutyala,A.V. Sumant,V.N. Mochalin, Materials Today Advances, Elsevier, March 2021),https://doi.org/10.1016/j.mtadv.2021.100133.
Creative Commons Attribution-Non-Commercial-No Derivatives 4.0 International (CC BY-NC-ND 4.0)
Figure 7 (a and b) display the friction test results of graphene, Ti3C2, and Ti3C2/graphene coatings, respectively, on Si substrates tested against DLC. The average friction coefficient for graphene vs. DLC was 0.0138 ± 0.0014 (700-3600 s), while for the Ti3C2/graphene (~37 wt% of graphene) coating, it was reduced to 0.0042 ± 0.0011. (700-3600 s), which not only reached the superlubricity range but indeed reduced the wear of the DLC ball significantly. The lower friction coefficient of Ti3C2/graphene against DLC could be attributed to the additional shearing and covering of MXene by graphene during the sliding process thereby reducing wear on the DLC side. It is also possible that graphene may have helped in passivating the reactive surface of MXene during friction.
Figure – 7:(a) Tribologicalbehavior of graphene, Ti3C2, and Ti3C2/graphene coatings against DLC-coated steel balls and (b) comparison of the corresponding COF values. Error bars represent standard deviations of average COF values. (Achieving superlubricity with 2D transition metal carbides (MXenes) and MXene/graphene coatingsS. Huang,K.C. Mutyala,A.V. Sumant,V.N. Mochalin, Materials Today Advances, Elsevier, March 2021),https://doi.org/10.1016/j.mtadv.2021.100133.
Creative Commons Attribution-Non-Commercial-No Derivatives 4.0 International (CC BY-NC-ND 4.0)
In essence, the addition of graphene to Ti3C2 further reduced the friction by 37.3% and wear by the factor of 2 as compared to Ti3C2 alone, while the superlubricitybehavior of the MXene remains unchanged. These results open up new opportunities for exploring the family of MXenesfor various tribological applications.
Credit: Pixabay/CC0 Public Domain
These newly discovered superlubric (solid lubricant) MXenes materials are of special interest for advanced anti-wear and lubrication applications in extreme extraterritorial environment like those encountered by the Perseverance rover on Mars (Newly discovered material may ease wear and tear on extraterrestrial vehicles).
In the study conducted by L. Guo, (MXene-Al2O3 synergize to reduce friction and wear on epoxy-steel contacts lubricated with ultra-low sulfur diesel) friction and wear properties of epoxy filled with 2D layered Ti3C2Tx and/or 0D Al2O3 were researched with the lubrication of ultra-low sulfur diesel (ULSD).Especially, the structure-property relationship of tribofilm formed in situ was studied. Conclusions are as follows:
(1) EP resin with the addition of few 2D layered Ti3C2Tx (3 wt%) exhibits low friction (0.13 at steady state) and wear under mixed/boundary lubrication. In particular, the tribological performance was further enhanced by adding Al2O3 nanoparticles into Ti3C2Tx reinforced EP resin. Most strikingly, the super-lubricity (COF was around 0.01) was realized in macroscale and the wear rate was reduced by more than 97%. A conclusion can be drawn that there exists a synergistic effect of MXene and nanoparticles in enhancing the friction and wear performance of the EP resin. Thus, the hybrid composite 3 Al2O3 / 3 Ti3C2Tx /EP is considered to be the candidate additive material lubricated by ULSD.
(2) The above result confirmed that the tribofilm with nanostructure consists of EP resin, 2D layered MXenes, rigid nanoparticles and graphitic crystals embodies the characteristics of high load bearing capability and easy-shearing. Moreover, the tribofilm was affirmed to separate the friction pairs effectively with the thickness of around 100 nm under the boundary and mixed lubrication resulting in substantially low friction and wear.
(3) The present work paves the way for hybrid polymer composites consist of different dimensions nanofillers that are far superior in tribological property compared to pure resin. The 2D layered structure, combined with rigid nanoparticles, is responsible for the extremely low friction and wear.
MXene as an Additive to Composites/Nanocomposites
MXenes imparts superior mechanical properties to polymer based composite materials (Preparation, mechanical and anti-friction performance of MXene/polymer composites). Due to a rich and diverse chemistry, MXenes have a great potential as a reinforcement for a variety of polymers. In recent times, MXenes have been used in many polymeric matrices such as nylon-6, polyurethane (PU), polylactic acid (PLA), polyacrylic acid (PAA), polyvinyl alcohol (PVA), polyvinylidene fluoride (PVDF), bisphenol F, chitosan, among others (Mechanotribological Aspects of MXene-Reinforced Nanocomposites).
In the work carried out by H. Zhang et al. (Preparation, mechanical and anti-friction performance of MXene/polymer composites) a Ti3C2 nanomaterial and Ti3C2/UHMWPE (ultrahigh molecular weight polyethylene) nanocomposites were prepared by simple hot-pressing technique. The morphology, structure and properties of the Ti3C2/UHMWPE nanocomposites were investigated. The addition of Ti3C2leads to a higher degree of crystallinity in the UHMWPE which resulted in lower friction coefficient (Friction and wear behavior of ultra-high molecular weight polyethylene as a function of polymer crystallinity). It was found that the hardness of the Ti3C2/UHMWPE nanocomposite increases with the increase in Ti3C2content. The Ti3C2/UHMWPE composites showed enhanced hardness, yield strength and creep resistance as compared to pure UHMWPE. The frictional properties of the Ti3C2/UHMWPE composites were studied using a pin-on-disc tester. The Ti3C2/UHMWPE composites exhibited a better friction-reducing performance in comparison with pure UHMWPE. The addition of Ti3C2can reduce the adhesive wear and ploughing friction, which results in the worn surfaces of the Ti3C2/UHMWPE composite being smoother than those of pure UHMWPE.
In another work, H. Zhang et al. investigated effects of an addition of 2-D transition metal carbide Ti2CTx on the properties of epoxy composites (Effects of 2-D transition metal carbide Ti2CTx on properties of epoxy composites). Apart from the improvement of various mechanical properties, their results on tribological characteristics indicated that there was a significant increase in anti-friction properties and the morphology of worn surfaces of the nanocomposites appeared to be smoother in nature than that of pure epoxy, which implied the transformation of fatigue and abrasion wear into adhesive wear. This work is of great importance in that novel 2-D transition metal carbide crystals were employed to fill and modify a thermoset polymer resin and enhance its toughness and strength and, as a self-lubricating additive, enabled a major breakthrough in the anti-friction properties of polymer-matrix composites.
In another work, the Ti3C2/graphene hybrid (M-G) with wrapping structure was successfully prepared by H. Yan et al. and as a fillerand it was added into epoxy coating (MG-EP). The results have shown that the epoxy composite reinforced by the combination of -OH terminated Ti3C2 MXene and graphene sheets (MG-EP) could dramatically reduce the wear rate, and that this wear reduction is not only very significant than the neat epoxy (pure-EP) but even also much greater than those samples filled by one of the graphene (G-EP) or MXene (M-EP) reinforcing agents (Towards high-performance additive of Ti3C2/graphene hybrid with a novel wrapping structure in epoxy coating).
The enhancement in wear behavior is probably due to the high load-bearing capacity of 2D reinforcing agents, the wrapping structure of MXene and graphene, the excellent thermal and tribological properties of 2D MXenes and graphene, as well as those tribofilmspresent between the mating surfaces during the wear tests. It is evident that the wear rate of the neat epoxy is nine times greater than the MG-EP coating nanocomposite. Moreover, the composite coating can retain good anticorrosion properties in corrosive medium during friction test, because its integrity prevents the diffusion of corrosive media.
The improved performance of composite coating mainly depends on: (a) the excellent lubrication and thermal conductivity of graphene and Ti3C2; (b) the synergistic effect of Ti3C2/graphene hybrid with wrapping structure; (c) the formation of protective film on the dual surface. The Ti3C2/graphene hybrid greatly enhances the tribological and anti-corrosive properties of organic coating, which opens a new avenue for the design and application of novel additives.
A variety of reinforcing agents, such as CNTs and graphene, have already been tested in metal matrices; however, agglomeration and poor wettability have been challenging problems in metal matrix composites (Advanced Metal Matrix Nanocomposites).MXenes have not only superior mechanical properties, but also contain rich hydrophilic surfaces ((e.g., Ti3C2Txhas a contact angle of 35°(Flexible and conductive MXene films and nanocomposites with high capacitance)), which render them asdesirable reinforcing agents for the purpose of strengthening metallic materials such as Cu, Al, etc. (Mechanical properties and frictional resistance of Al composites reinforced with Ti3C2TxMxene).
Another important advantage of MXenes based metal matrix composites is the stability of Ti3C2Txin metals sintered at temperatures greater than 1000 °C, which illustrates MXenes’ potential to provide a nanolamellar transition metal carbide reinforcing material for metals with high melting points, such a stable behavioris not possible for carbonaceous nanomaterials such as graphene which can turn into undesired phases when exposed it toelevated temperatures (Graphene–aluminumnanocomposites).
In the study undertaken by J. Hu et al. (Mechanical properties and frictional resistance of Al composites reinforced with Ti3C2Tx MXene) 2D Ti3C2Txwas used to enhance the mechanical and frictional properties of Al matrix composites. Ti3C2Tx/Al composites were designed and prepared by pressureless sintering followed by hot extrusion technique. The prepared composites exhibit a homogeneous distribution of Ti3C2Tx and forms strong bonding interfaces in the composites. The Vickers hardness and the tensile strength continuously increase with increasing Ti3C2Txcontent. A hardness of 0.52 GPa and a tensile strength of 148 MPa (≈65% improvement) were achieved in the 3 wt% Ti3C2Tx/Al composite. The comparative frictional properties of pure Al and the Ti3C2Tx/Al composite were studied under dry sliding conditions. A low friction coefficient of 0.2 (≈200% reduction), was achieved in the 3 wt% Ti3C2Tx/Al composite. Ti3C2Txacting as a solid lubricant reduces the abrasive wear in the composite, while improving the frictional properties of Al matrix composites.
Mai et al. (Self-lubricating Ti3C2 nanosheets/copper composite coatings) could prepare a self-lubricating Ti3C2-reinforced copper matrix composite using an electrodeposition technique, wherein they found that the addition of MXenenanosheets considerably improved the tribological characteristics. The values of friction coefficient and the wear rate of neat sample were found to be 0.5 and 70.7 × 10−5 mm3 N−1 m−1, respectively. On the other hand, the value of friction coefficient for the 26- Ti3C2 /Cu composite was 0.27 corresponding to 46% reduction as compared to the MXene-free sample; the wear rate reached to 3.7 × 10−5 mm3 N−1 m−1, being 19 times lower than the sample with the presence of MXene reinforcement. These results are comparable with those achieved from the composites reinforced by graphene oxide (Surfactant-free electrodeposition of reduced graphene oxide/copper composite coatings) with enhanced wear resistance or graphite (Wear and friction characteristics of electrodeposited graphite–bronze composite coatings) by the same manufacturing method
Conclusion
In the present article we have provided an overview of mechanical and tribological behaviour of MXenes and MXene-based nanocomposites. The article discusses MXenes as dry lubricant films, liquid lubricant additives as well as composite additives. The topic of super lubricity has also been expounded in great detail. Additionally, the article has also presented a critical perspective of the compositional control of MXenes for achieving structural, low-friction, and low-wear performance in current and emerging applications of MXenes.
MXenes and MXene-based nanocomposites have extremely bright prospects and can be further explored in the different horizons of science and technology from atomistic to macroscopic scales in all theoretical, computational, and experimental investigations. Still, a great deal of effort is required to well characterize and then optimize the properties of MXenes and MXene-based nanocomposites, finally leading to materials with superior targeted properties.
About Author
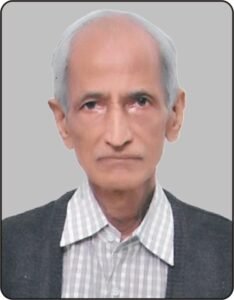
Dr Yashwant R Mahajan is presently Honorary Editor of Nanodigest website portal. Earlier, he was Technical Advisor at International Advanced Research Centre for Powder Metallurgy and New Materials (ARCI), Hyderabad. He obtained his Ph.D. degree in Physical Metallurgy in 1978 from Polytechnic Institute of Brooklyn, New York. He has worked in various capacities, namely, Scientist/Joint Director at the Defence Metallurgical Research Laboratory, ARCI, and Defence Research and Development Laboratory, Hyderabad, India, and Hindustan Aeronautics Ltd., Bangalore, India. Dr Mahajan made major contributions in the areas of MMCs, advanced ceramics, and CMCs. Under his leadership, a number of ceramic- based technologies were developed and transferred to the industry. He has published more than 130+ technical papers in peer-reviewed journals and conference proceedings and holds 13 patents (including 2 US). Dr Mahajan had initiated and successfully implemented a number of programs concerning selection and application of advanced materials for defence applications, which includes Development of Infrared Domes and Windows Based on Transparent Ceramics, SiAlONRadomes for Hypersonic Missile Applications, Ultra-High Temperature Materials for the Airframe and Scramjet Engine of Hypersonic Technology Demonstrator Vehicle, Reaction Bonded Silicon Carbide Thrust Bearings for Naval Application, and Silicon Carbide Based Mirror Substrates for Satellite Application.
email: mahajanyrm@gmail.com