By Dr Yashwant Mahajan
Introduction and Background
Orbital debris (space junk) (Figure 1) are fragments (typically millimeter sizes particles) disintegrated from launched objects like spacecraft orbiting around the earth. Humans have been launching objects into space for more than 50 years. Most of those objects have fallen back to Earth.
Figure 1-A spot of space debris illuminates in the night sky. Source: https://www.flickr.com/photos/lonetown/4756669967/Author: Bob MacInnes, (Creative Commons Attribution 2.0 Generic).
In addition,micrometeorites can also collide with spacecraft and satellites potentially causing serious damage or catastrophic failure. These collisions can be a life-threatening hazard to astronauts conducting extra-vehicular activities in space. The mean debris velocity is about 10 km/s (36,000 km/h) (Frequently Asked Questions: Orbital Debris) in low earth orbit (LEO). Therefore, the need of the day is to develop an effective shield against hyper velocity particles to sustain any space exploration mission. Moreover, the shielding solutions should be within the allocated mass, volume, and cost budgets of the spacecraft.
In this regard, The Whipple Shield (Advances in the Whipple Shield Design and Development) is the first spacecraft shield ever implemented. It was introduced by Fred Whipple (Meteorites and space travel) back in the 1940s, and is still in use today.The dramatic representation of the effectiveness of Two-Layer Whipple Shield in providing protection from hyper velocity impact to the single layer monolithic target is quite evident as shown in Figure 2 (Micrometeoroid and Orbital Debris Environment & Hyper velocity Shields).
Figure 2-A Two-layer Whipple Shield provides more effective protection from hyper velocity impact than single layer (total shield thickness < projectile diameter). Source: PPT presentation by Eric L. Christiansen and Dana M. Lear.Courtesy: NASA
The simplest kind of Whipple shield consists of a bumper, such as a thin sheet of aluminium, and a standoff, or open space, between the bumper and the wall of the spacecraft. The function of bumperis to break up the projectile into a cloud of material containing smaller, and less lethal fragments of bumper and projectile. This would allow the full force of the debris cloud to be diminished over a larger area on the spacecraft rear wall. For most conditions, a Whipple shield results in a significant weight reduction over a single plate, otherwise which must contend with deposition of the projectile kinetic energy in a very localized area (Figure 3).
Figure 3-Conventional Whipple shield design: (left) Whipple shield configuration, (centre) post impact debris cloud formation and (right) effects of impact on rear plate. Reference: Adopted from Handbook for Designing MMOD Protection.Courtesy: NASA
Other advanced shielding design concepts developed to enhance shielding performance include the Stuffed Whipple Shield, the Multi-Shock Shield, the Mesh Double Bumper Shield, aluminium honeycomb sandwich panel structures, metallic foam sandwich panels and the Mars Module Shield (Transhab).Some of the shielding materials used in these designs are Nextel woven ceramic fabric, Kevlar or combination of Kevlar and Nextel, aluminium alloys Al 6061 and Al 2219, Beta cloth in the form of multi-layer insulation, aluminium mesh or honeycomb, steel mesh and aluminium foam sandwich panels (Hypervelocity Impact Technology).
Based on the studies carried out at NASA, USA and DSTO, Australia the researchers inserted low-density impact-resistant materials in the open spacing of the Stuffed Whipple shields to reduce the speed or capture secondary debris clouds in their microstructures (Hypervelocity impact testing of advanced materials and structures for micrometeoroid and orbital debris shielding) . In their investigation, they have found for the hyper velocity impact condition, potential weight savings of at least 47% over conventional all-aluminium Whipple shields are feasible by utilizing the investigated materials and structural concepts.Incorporation of low-density impact-resistant materials as an augmentation for interior shield offers an increase in the ballistic performance of the stuffing materials. This strategy results in a decrease of the thickness of the heavy metal rear wall of the shield system as well as a minimization in the stand-of spacing between the Whipple bumper and back plate, which has potential to achieve significant mass and volume savings.
Figure 4-This artist’s concept shows the Stardust spacecraft beginning its flight through gas and dust around comet Wild 2. The white area represents the comet. The sample collector is the tennis-racket-shaped object extending out from the back of the spacecraft. Credit: NASA/JPL
Figure 5-Comet dust collector with aerogel. Courtesy: JPL, NASA. Credit: Stardust Outreach Team: Aimee Whalen, Ron Baalke, James D. Rose
The NASA’s Stardust mission was the first to collect particles from a comet (81P/Wild2, a Jupiter family comet) and interplanetary dust (Figure 4and 5) (Catching Comet Dust with Aerogel).Thousands of cometary and interplanetary particles were collected by trapping them into silica aerogel and brought to earth through NASA’s Stardust Mission. It is of interest to note that although the size of the collected particles and debris were only a few tens of microns, these studies have suggested the high potential ballistic containment feasibility in aerogel materials. Incidentally,pristine silica aerogel derived from tetramethoxysilane (TMOS) with a density of ~ 0.12 g/cm 3 can be easily destroyed under a stress of~ 31 kPa (Reinforcement of Silica Aerogels Using Silane-End-Capped Polyurethanes). This failure at relatively low stress is an effect of its “pearl necklace” structure and is attributed to spherical secondary silica particles joined to each other by only a few Si-O-Si bonds, are responsible for the fragility of native silica aerogels.
However, despite its fragile nature and very low mechanical properties, aerogel is an excellent hypervelocity space debris capture medium due to the fact that it is a highly porous material with a tortuous microstructure made up of nanoscale particles forming aggregatesas well as their high specific surface areas. When a debris or a particle impacts the aerogel as the aggregates are crushed, the micron-sized spherical debris are slowed down and finally stopped (the tortuous structure of the aerogel dissipates its kinetic energy) (Aerogels Materials as Space Debris Collectors).However, brittle silica aerogels are not that effective to contain millimeter-sized debris that areimpinging upon the spacecraft with extremely high kinetic energy due to their inherent poor mechanical properties.
Emergence of polymer aerogel led to a paradigm shift in our outlook on the mechanics of aerogel materials(Polyimide aerogels for ballistic impact protection). Polymer aerogels, especially polyimides (PIs) show a resistance to compression and tensile stress more than 100 times higher than silica aerogels. In terms of flexibility, the new class is very similar to synthetic rubber, but at a mere 10% of its weight. They also exhibit excellent mechanical properties as compared to silica and polymer–silica hybrid aerogels (Tailoring Mechanical Properties of Aerogels for Aerospace Applications,). Particularly, PI aerogels cross linked with OAPS and TAB display higher strength at similar density than silica aerogeland polymer reinforced silica, and they also perform favourably well with polymer (PU) foams (Polyimide and Polyamide Aerogels) (Figure 6).
Figure 6 -Polyimide aerogels are stronger than silica and polymer reinforced silica aerogels. Octahedral oligomeric silsesquioxane (OAPS), 1,3,5-triaminophenoxybenzene (TAB), Polyimide (PI), Polyurethane (PU). Courtesy: NASA
Among many aerogels based on polymers (For example,phenolic resins, polybenzoxazine, polyurethane, polyurea, epoxy etc.) high-performance polyimide aerogels have been implemented in various aeronautics and space applications due to their strong mechanical properties (Figure 6) and ability to maintain structural integrity at high temperaturesof up to 400 Celsius degrees and higher. The new class of polyimide aerogel however couldn’t be manufactured by conventional methods being used as on date. The team of researchers adopted a cross-linking approach, where linear polyamides were reacted with a bridging compound to form a three-dimensional covalent polymer. The resulting density of the polymer aerogel was 0.14 g/cc, with 90% porosity.One can imagine that this new polyimide material could have an impact upon the practically a wide range of applications(New polymer aerogels might become the wonder insulating material).
The typical SEM micrograph displaying nano-scaled microstructure is shown in Figure 7. However, the pore structure of polyimide is susceptible to heat shrinkage, which increases its density and thermal conductivity. To alleviate this problem associated with pore defect,cross-linked polyimide aerogels have been developed. The key for preparing cross-linked aerogel is the use of crosslinkers. At present, the cross-linkers of polyimide are mainly organic small molecules including Octahedral oligomeric silsesquioxane (OAPS), 1,3,5-triaminophenoxybenzene (TAB),2,4,6-tris (4- aminophenyl) pyridine (TAPP) (Study on Thermal Conductivities of Aromatic Polyimide Aerogels).
Unluckily, the preparation technique of these molecules is complex and tedious, and the raw materials are expensive. (Poly (maleic anhydride) cross-linked polyimide aerogels: synthesis and properties) Furthermore, most of them are harmful to humans and the environment. Therefore. the candidates with multiple amino or carboxyl properties have elicited the attention of researchers. BTC is a cost-effective commercially available alternative toTAB, TAPP, orOAPS. Aerogels made in this way have the same or higher modulus and greater surface area compared to those previously reported with either TAB or OAPS cross-links at the same density (A Low-Cost Alternative for Mechanically Strong Polymer Aerogels).
Figure 7-Scanning electron micrograph of the nano-sized cell structure of NASA’s new polymer aerogel. The average cell size is about 10 nanometers. Photo Courtesy: NASA
All polymer crosslinked aerogels have extremely high specific energy absorption capabilities, reaching values as high as 192 J/g in compression (Structural Characterization of Aerogels).NASA’s Glenn Research Center synthesized polyimide aerogels by cross-linking through an aromatic triamine (Mechanically Strong, Flexible Polyimide Aerogels Cross-Linked with Aromatic Triamine) or polyhedral oligomeric silsesquioxane, and chemically imidizing at room temperature.
Figure 8- Flexible polyimide aerogel cast into half a millimetre thick sheet. (Source: Tech Brief- Polyimide Aerogels Boost Antennas, Insulate Pipes. Courtesy: NASA
The resulting product is a cross-linked polyimide aerogel that retains the positive characteristics such as flexibility and strength of polyimide materials, and adds the beneficial properties of aerogels without replicating the brittle and fragile nature of silica aerogels (Polyimide Aerogels with Three-Dimensional Cross-Linked Structure).One of the most important attributes of these polyimide aerogels is that they can be produced into thin strips which don’t break down, allowing for insulation of sensitive parts (Figure 8).
Experimental Procedure, Results and Discussion
In view of the above mentioned background, the primary objective of this work is to evaluate the ballistic performance of these mechanically robust polyimide aerogels through a series of ballistic impact tests at a number of velocities. The experiments were carried out using a helium-filled gas gun connected to a vacuum chamber and a spherical steel projectile (3.175 mm diameter). Figure 9 schematically exhibits the layout of the gas gun. The impact velocity of the projectile was ranging between 150-1300 ms-1. The study is undertaken with the purpose that the outcome of this work will aid in the design and manufacturing of new advanced stuffed Whipple shield systems for future space exploration missions.
Figure 9- (A) A schematic showing the main components of the helium-filled gas gun connected to a vacuum chamber. Malakooti, S., Vivod, S.L., Pereira, M. et al. Polyimide aerogels for ballistic impact protection. Sci Rep 12, 13933 (2022). https://doi.org/10.1038/s41598-022-18247-z Creative Commons Attribution 4.0 International (CC BY 4.0)
Accordingly, the polyimide gels were synthesized by a sol–gel process taking stoichiometric amounts of pyromellitic dianhydride (PMDA) and 2,2′-dimethylbenzidine (DMBZ) in N-methyl-2-pyrrolidone (NMP) to create a solution of polyamic acid oligomers. These oligomers were imidized by chemical means at room temperature using acetic anhydride (AA) as a water scavenger and triethyl amine (TEA) as a base catalyst. The oligomeric solutions be turned into gels via the addition of a small amount of cross-linker (BTC). As mentioned earlier the 1,3,5-benzenetricarbonyl trichloride (BTC)is a cost effective, lower cost, commercially available alternative to TAB, TAPP, or OAPS. Aerogels made in this way have the same or greater modulus and more surface area compared to those previously reported with either TAB or OAPS cross-links at the same density.
While the cross-link structure is an amide, the thermal stability is not compromised most likely because the cross-link is only a small part of the composition of the aerogel (Polyimide Aerogels with Amide Cross-Links: A Low-Cost Alternative for Mechanically Strong Polymer Aerogels). When the cross-linking agent is added, the solution can be cast in a variety of forms such as thin films and monoliths. To remove the solvent, one or more solvent exchanges can be performed, and then the gel is subjected to supercritical drying to form a polyamide aerogel. In the final step, the aerogel polyimide was then amorphously and isochorically frozen below room temperature and subsequently sublimed under a flow of dry gas at atmospheric pressure, eliminating the need for a vacuum vessel.
A number of polyimide aerogel samples were prepared and their bulk density, porosity, shrinkage, and the actual thicknesses were measured. The mean bulk density and the skeletal density of the samples were measured and were found to be 0.17 g cm−3 and 1.46 g cm−3, respectively. The average total linear shrinkage of the samples relative to their moulds was 18.8%.Based on the skeletal and bulk densities, the porosity of the samples was calculated and was found to be ranging between 88.3% and 90%.
The morphological, and chemical characterization was carried out using SEM, FTIR and TGA. Figure 10 shows the SEM images of a polyimide aerogel sample with an areal density of 0.17 g/cm3 at two different magnifications. The aerogel micrographs display a highly entangled and tortuous nanofibrous microstructure with an average fiber diameter of 11.37 nm. The fiber diameter size distribution is shown as an inset in Fig. 10. Based on N2-sorption measurements it was determined that the aerogels are mainly mesoporous in nature with a high specific surface area of about 566 m2 g−1. The average pore size of the aerogels is 16.84 nm as determined by using BJH desorption model. Nanofibrous microstructure plays an important role in the energy dissipation performance.
For example, in glassy polymers above a critical entanglement density, the main energy dissipation mechanism arises from inter molecular disentanglement and molecular degradation of a polymer main chain leading to enhanced strength and toughness or the energy dissipated by deforming a sample to failure (Load-bearing entanglements in polymer glasses). Therefore, polymeric systems possessing highly entangled nanofibrous microstructures, as in the case of present study, typically surpasses their counterparts with particulate microstructures involving mechanical energy absorption applications including impact energy attenuation.
Figure 10-Representative SEM micrographs at two different magnifications for the polyimide aerogels with 0.16 g/cm3 bulk density (n= 40, 10% w/w). The fiber diameter size distribution of the aerogel is also shown in the inset.Malakooti, S., Vivod, S.L., Pereira, M. et al. Polyimide aerogels for ballistic impact protection. Sci Rep 12, 13933 (2022). https://doi.org/10.1038/s41598-022-18247-z. Creative Commons Attribution 4.0 International (CC BY 4.0)
Using FTIR spectroscopy, the nature of chemical bonds of the polyimide aerogels were established.Based on the FTIR spectra,chemical constituents present in the aerogel are identified and are elucidated in the paper on Polyimide aerogels for ballistic impact protection.The interested readers may like refer to this paper for accessing further details on this aspect.
The Young’s modulus of the aerogels at a low strain rate (i.e., 0.01 s–1) was also determined at room temperature and it was found to be 139MPa at bulk density of 0.16 g cm−3. This modulus is considered to be quite high for a such a low-density material which simply outperformshigh density silica aerogel where the modulus is only 2.4 MPa at the bulk density of 0.25 g cm-3(specific modulusis0.096106 m2 s−2).The specific modulus of polyimide aerogels (i.e., modulus per unit density) is 0.87 × 106 m2 s−2which is three orders of magnitude higher than the corresponding values for typical high density polymeric foams such as latex foam (0.0002 × 106 m2 s−2) and twice as high as state-of-the-art aluminum foams, such as Duocel® (0.47 × 106 m2 s−2), at a similar bulk density (Approximate specific stiffness for various materials). Incidentally, atlow impact velocities, the aerogels failed by ductile hole enlargement followed by a tensile failure. By contrast, at high impact velocities, the aerogels failed through an adiabatic shearing process.
The measured projectile impact and exit velocities and the aerogels absorbed energy percentage at different velocities are shown schematically in Figure 11 (a and b). The ballistic limit velocity of the aerogels is ranging between 175 and 179 m s-1(Figure 11 a). Within the range of the projectile impact velocities covered in this study, the ballistic performance of the aerogel’s samples exhibits two regimes (Figure 9 b). In the initial stage, by increasing the projectile impact velocity up to about 900 m s-1, the absorbed energy plummets down as the projectile penetrates through the aerogels’ blocks without additional energy absorption by tensile stretching. As shown in Figure 11b, beyond 900 m s-1, the absorbed energy increases to only a small extent due to the fragmentation of aerogel sample and possibly its partial melting. The front and back faces of the aerogel block impacted by a projectile with a speed of 921.65 m s-1 displaying the target fragmentation are depicted in the inset of Figure 11 b. Overall, the aerogels show a minimum 20% energy absorption capacity in this study.
Figure 11 a- Measured projectile velocity exit velocity as a function of projectile impact velocity showing the ballistic limit velocity rangeMalakooti, S., Vivod, S.L., Pereira, M. et al. Polyimide aerogels for ballistic
impact protection. Sci Rep 12, 13933 (2022). https://doi.org/10.1038/s41598-022-18247-z) Creative Commons Attribution 4.0 International (CC BY 4.0)
Figure 11 b- The ballistic energy absorption performance of the polyimide aerogel blocks as a function of the projectile impact velocity. The inset displays the front and back faces of the aerogel block impacted by a projectile with a speed of 921.65 m s-1.Malakooti, S., Vivod, S.L., Pereira, M. et al. Polyimide aerogels for ballistic impact protection. Sci Rep 12, 13933 (2022). https://doi.org/10.1038/s41598-022-18247-z. Creative Commons Attribution 4.0 International (CC BY 4.0)
Concluding Remarks
Space debris and meteoroids cause a potent hazard to space exploration activities as a result of hyper-velocity impacts causing major damage to spacecrafts, satellites and other space assets in the lower earth orbit (LEO). In order to cope up with the impact caused by space debris travelling at hyper-velocities, Fred Whipple invented the” Whipple shield” in the 1940s. However, still there is a greater need to develop shields with improved performance by employing advanced materials designed for orbital debris containment that are lightweight and reduced volume that offer confinement to debris cloud, velocity deceleration and kinetic energy absorption. Current materials within a shield system for either containment during critical impact or energy dissipation require complex functional supports associated with significant mass, higher bulk density and larger volume (Hypervelocity impact testing of advanced materials and structures for micrometeoroid and orbital debris shielding). Therefore, there arises a need to reduce cost, weight, and volume together to sort out the multiple issues with debris remediation.
To resolve this issue the potential of lightweight and mechanically strong polyimide aerogels is investigated by carrying out a series of ballistic impact tests at various velocities, from 150 to 1300 m s−1, using a helium-filled gas gun connected to a vacuum chamber and a spherical steel projectile.The ballistic limit velocity of the aerogels was estimated to be in the range of 175–179 m s−1. Moreover, the aerogels showed a robust ballistic energy absorption performance (e.g., at the impact velocity of 1283 m s−1 at least 18% of the impact energy was absorbed). As a low-density impact-resistant material, these aerogels exhibit a great potential to be used as a stand-off spacing material in the stuffed Whipple shields to decelerate/capture secondary debris clouds. This would potentially lead to significant mass and volume savings in these shielding systems. Their other potential applications span areas with ballistic remediation requirements such as military helmets and shielding sensitive equipment.
About Author
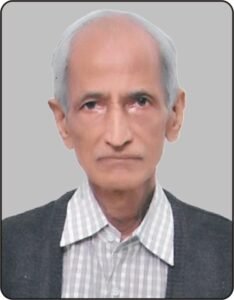
Dr Yashwant R Mahajan was Technical Advisor at International Advanced Research Centre for Powder Metallurgy and New Materials (ARCI), Hyderabad. He obtained his Ph.D. degree in Physical Metallurgy in 1978 from Polytechnic Institute of Brooklyn, New York. He has worked in various capacities, namely, Scientist/Joint Director at the Defence Metallurgical Research Laboratory, ARCI, and Defence Research and Development Laboratory, Hyderabad, India, and Hindustan Aeronautics Ltd., Bangalore, India. Dr Mahajan made major contributions in the areas of MMCs, advanced ceramics, and CMCs. Under his leadership, a number of ceramic- based technologies were developed and transferred to the industry. He has published more than 130+ technical papers in peer-reviewed journals and conference proceedings and holds 13 patents (including 2 US). Dr Mahajan had initiated and successfully implemented a number of programs concerning selection and application of advanced materials for defence applications, which includes Development of Infrared Domes and Windows Based on Transparent Ceramics, SiAlONRadomes for Hypersonic Missile Applications, Ultra-High Temperature Materials for the Airframe and Scramjet Engine of Hypersonic Technology Demonstrator Vehicle, Reaction Bonded Silicon Carbide Thrust Bearings for Naval Application, and Silicon Carbide Based Mirror Substrates for Satellite Application. He is presently Editorial Advisor to Nano Digest.
Email: mahajanyrm@gmail.com